Functional Artist
- Jul 21, 2018
- 18
- Joined
- Jul 21, 2018
- Messages
- 18
I am working on a go kart that will have a 60V propulsion system.
I just found/bought a Boma 60V 2,000W brushless motor & controller combo from Alfa Wheels. ($250.00) https://www.ebay.com/str/alfawheels1
I have worked with 12V, 24V, 36V & 48V systems, but 60V is new to me.
I have used (12V) automotive fuses many times without problems, but to use them on a 60V seems to be "pushing it".
I have also used marine style circuit breakers, but they are usually rated @ 48V max.
The current specs. on this 60V controller says, 35A.
What is the Rule of thumb or guidelines on the proper & safe use of fuses & circuit breakers? tips? or suggestions?
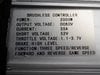
I just found/bought a Boma 60V 2,000W brushless motor & controller combo from Alfa Wheels. ($250.00) https://www.ebay.com/str/alfawheels1
I have worked with 12V, 24V, 36V & 48V systems, but 60V is new to me.
I have used (12V) automotive fuses many times without problems, but to use them on a 60V seems to be "pushing it".
I have also used marine style circuit breakers, but they are usually rated @ 48V max.
The current specs. on this 60V controller says, 35A.
What is the Rule of thumb or guidelines on the proper & safe use of fuses & circuit breakers? tips? or suggestions?
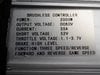